An overview of mechanical seal failure causes of pumps
The measure for preventing the leakage of the working medium from the pump, or preventing the intrusion of foreign matter or air into the interior of the pump is called sealing, and the media to be sealed are generally liquid, gas or powder. There are two main types of pump sealing: one is static sealing and the other is dynamic sealing. Static sealing is usually available in gasket seals, O-ring seals, thread seals, etc. Whereas the dynamic sealing mainly includes soft packing seals, oil seals, spiral seals, mechanical seals. There are two reasons for pump leakage. First, there is a gap in the sealing surface. Second, there is a pressure difference on both sides of the sealing part. Eliminating or reducing any one factor can prevent or reduce leakage and achieve the purpose of sealing. The design pressure and the use pressure of the pump are objectively and cannot be reduced, so the sealing of the pump solves the problem of eliminating or reducing the gap between the sealing faces. Such gaps include the gap between the sealing faces and the gap within the body of the seal.
Mechanical seals are the primary method of modern pump shaft seals, although it is not easy to use them to achieve complete leakproofness, it is entirely possible to achieve fully acceptable sealing performance. However, in the operation of the pump, there are often some tricky situations, so what are the causes of mechanical seal failure?
Causes of mechanical seal failures
The material of the mechanical seal does not match the medium being conveyed. During use, the sealing element is quickly corroded, dissolved or worn, thus losing its sealing ability. Because of this, the choice of the material of the mechanical seal according to the properties of the medium is a prerequisite for ensuring its sealing function and service life.
The condition of the mechanical seal during flushing does not meet the design requirements. When transporting a medium that is easy to crystallize or has fine particles, it must be flushed with a certain pressure and certain flow of flushing liquid. Otherwise, the crystal or particles will accelerate the wear of the sealing pair and affect the automatic compensation of the sealing pair after wear and leakage. Therefore, according to the properties of the medium, it is necessary to configure not only the corresponding pipeline for flushing, but also the instrument and device with monitoring and regulating functions to ensure that the pressure and flow of the flushing fluid meet the design requirements.
The pressure that each mechanical seal can withstand is limited. Because the pressure in the sealing cavity is not accurate, the pressure in it exceeds the level that the mechanical seal can withstand, resulting in leakage. It is also one of the common causes of seal failure.
The working temperature of the mechanical seal cannot exceed its specified value. In the design of the cooling pipeline, the cooling effect is often reduced due to insufficient flow of the cooling medium; while in the design without the cooling pipeline, the mechanical seal is often in a dry friction state due to the air trapped in the sealing cavity. In both cases, the operation temperature of the seal is too high to withstand and accelerated wear, resulting in seal failure.
When using a single spring mechanical seal, it is easy to neglect the correct combination of the rotation direction of the spring and that of the pump rotor. Due to the design that is not stated, or the negligence during assembly, the spring force of the mechanical seal is decreased even the rotor is rotating, and as a result, the pressure of the friction pair of moving ring and static ring is insufficient and causes a leak.
The serious wear or damage of the bearing causes the pump shaft to produce severe axial movement. With the development of scientific technology, new sealing forms and sealing materials have emerged, which will inevitably have a direct impact on the pump sealing technology. Long-service-life, zero-leakage pump products will be promoted and applied in more and more places.
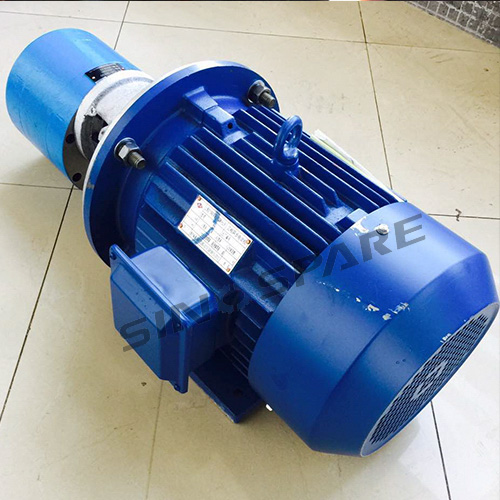
Mechanical seals are the primary method of modern pump shaft seals, although it is not easy to use them to achieve complete leakproofness, it is entirely possible to achieve fully acceptable sealing performance. However, in the operation of the pump, there are often some tricky situations, so what are the causes of mechanical seal failure?
Causes of mechanical seal failures
The material of the mechanical seal does not match the medium being conveyed. During use, the sealing element is quickly corroded, dissolved or worn, thus losing its sealing ability. Because of this, the choice of the material of the mechanical seal according to the properties of the medium is a prerequisite for ensuring its sealing function and service life.
The condition of the mechanical seal during flushing does not meet the design requirements. When transporting a medium that is easy to crystallize or has fine particles, it must be flushed with a certain pressure and certain flow of flushing liquid. Otherwise, the crystal or particles will accelerate the wear of the sealing pair and affect the automatic compensation of the sealing pair after wear and leakage. Therefore, according to the properties of the medium, it is necessary to configure not only the corresponding pipeline for flushing, but also the instrument and device with monitoring and regulating functions to ensure that the pressure and flow of the flushing fluid meet the design requirements.
The pressure that each mechanical seal can withstand is limited. Because the pressure in the sealing cavity is not accurate, the pressure in it exceeds the level that the mechanical seal can withstand, resulting in leakage. It is also one of the common causes of seal failure.
The working temperature of the mechanical seal cannot exceed its specified value. In the design of the cooling pipeline, the cooling effect is often reduced due to insufficient flow of the cooling medium; while in the design without the cooling pipeline, the mechanical seal is often in a dry friction state due to the air trapped in the sealing cavity. In both cases, the operation temperature of the seal is too high to withstand and accelerated wear, resulting in seal failure.
When using a single spring mechanical seal, it is easy to neglect the correct combination of the rotation direction of the spring and that of the pump rotor. Due to the design that is not stated, or the negligence during assembly, the spring force of the mechanical seal is decreased even the rotor is rotating, and as a result, the pressure of the friction pair of moving ring and static ring is insufficient and causes a leak.
The serious wear or damage of the bearing causes the pump shaft to produce severe axial movement. With the development of scientific technology, new sealing forms and sealing materials have emerged, which will inevitably have a direct impact on the pump sealing technology. Long-service-life, zero-leakage pump products will be promoted and applied in more and more places.
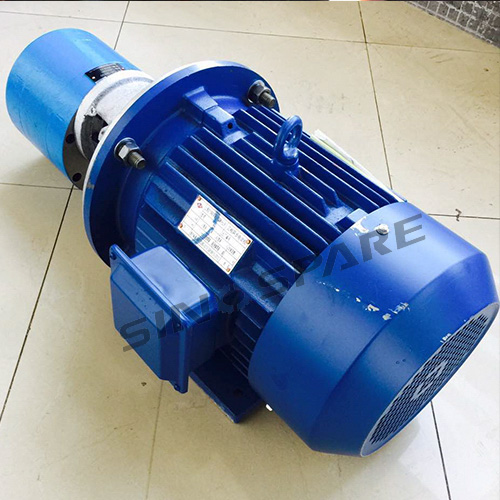