Fault causes and solutions of roller press - bearing damage
The four bearings of the roller press are the key parts of the whole machine. The grinding force of the crushing material of the roller press is applied to the bearing block by the hydraulic cylinder to push the roller and the motor is driven to rotate the press roller, which needs to be implemented by the bearing. Once the bearings are broken, the roller press has to be shut down.
The reasons for bearing damage are manifold:
1. Manufacturing quality problems of the bearing itself.
2. It may be caused by overload and increased load, such as setting the working pressure too high, the speed of the two rolls being not the same, the material being too thick, the amount of liquid fuel being not equal, etc.
3. The vibration is too severe and may cause bearing damage;
(1) The content of fine powder in the material is too much (for instance, the content of the material with grain size below 5 mm is more than 50%);
(2) The material of the roller press is too dense, and the discharged gas cannot be discharged through the upper material due to the decrease of the porosity when the material is formed into the dense feeding;
(3) When passing through the roller press, the feeding port of the roller press is blocked by foreign matter or the lower material is not uniform.
4. An improper installation which leaves hidden dangers, such as:
(1) The center line of the two rolls is not parallel or not at the same level;
(2) The limit stop between the two rollers is too thin, which may cause contact between the two rollers when idling;
(3) When installing, the required interference degree of the bearing clearance (0.25~0.35 mm) is not reached.
5. It is possible that the deviation of the roll gap at both ends is large and continuous operates for a long time.
(1) There is a problem with the control system, the pressure at both ends is not equal, and it cannot be adjusted for a long time;
(2) The problem of the material itself -- after the material enters the buffer bin, the segregation phenomenon of different degrees is generated. And after the material with uneven particle size distribution enters the roller press, the ends of the roller are unevenly stressed, and the deviation of the roll gap will be generated;
(3) One side of the lateral baffle fails, material throughput at both ends of the roller are uneven, the unrestricted side of the passage is large and the pressure is low;
(4) The deviation of the width of the inlet port along the direction of the roller is large or the side of the inlet is blocked by foreign matter, so that when the material passes through the gap between the two rollers, the throughput of the two ends of the roller is not equal.
6. Poor bearing cooling -- unsmooth cooling water circulation or insufficient cooling water may cause the bearing temperature to be too high and damaged.
7. For systems that use dry oil lubrication, bearing seal failure, insufficient dry oil supply, etc. may cause poor bearing lubrication and damage the bearing.
8. The oil deteriorates and the oil enters the ash, causing damage to the bearing.
To prevent bearing damage, do the following:
(1) Strictly control the quality when purchasing bearings;
(2) Ensure that the control system works normally and effectively;
(3) When the roller press starts feeding, it starts to add a certain pressure first. When the material pushes the roller press to open a certain roll gap, it starts to pressurize to the working pressure, so that the moving amount of the moving roller is not from the minimum to the maximum, which can effectively reduce vibration;
(4) When the bearing is installed, first, one must strictly control the interference of the bearing clearance; second, ensure that the centerline of the two rollers is parallel and at the same level; third, for different specifications of the roller press, the thickness of the stopper should also be different. When the roller press is idling, the two roller surfaces are not inconsistent. Generally speaking, it is suitable to be 18-30 mm;
(5) Regarding the working pressure, in theory, the best effective range is 30-150 MPa;
(6) In terms of materials, it is advisable to reduce the content of fine powder as much as possible, and the content of particles with a particle size of 20-25 mm need to be more than 60%;
(7) Take measures to control the deviation of the roll gap, such as adding a distributor in the upper part of the stable silo, adding the overflow box inside, and adding the insulation board in the warehouse;
(8) Ensure that the throughput of materials can be adjusted freely;
(9) Strengthening lubricant management and on-site management. Standard equipment management and a good environment are necessary to ensure the normal operation of the lubrication system.
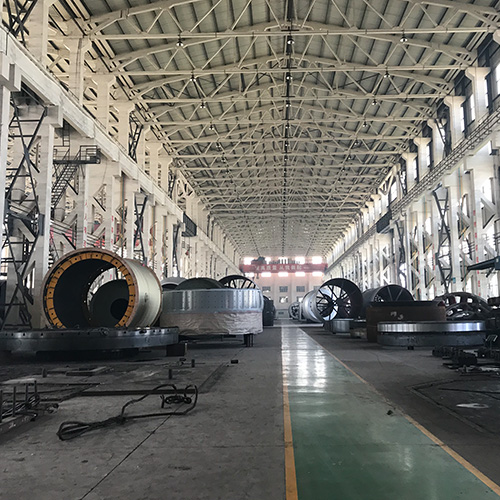
The reasons for bearing damage are manifold:
1. Manufacturing quality problems of the bearing itself.
2. It may be caused by overload and increased load, such as setting the working pressure too high, the speed of the two rolls being not the same, the material being too thick, the amount of liquid fuel being not equal, etc.
3. The vibration is too severe and may cause bearing damage;
(1) The content of fine powder in the material is too much (for instance, the content of the material with grain size below 5 mm is more than 50%);
(2) The material of the roller press is too dense, and the discharged gas cannot be discharged through the upper material due to the decrease of the porosity when the material is formed into the dense feeding;
(3) When passing through the roller press, the feeding port of the roller press is blocked by foreign matter or the lower material is not uniform.
4. An improper installation which leaves hidden dangers, such as:
(1) The center line of the two rolls is not parallel or not at the same level;
(2) The limit stop between the two rollers is too thin, which may cause contact between the two rollers when idling;
(3) When installing, the required interference degree of the bearing clearance (0.25~0.35 mm) is not reached.
5. It is possible that the deviation of the roll gap at both ends is large and continuous operates for a long time.
(1) There is a problem with the control system, the pressure at both ends is not equal, and it cannot be adjusted for a long time;
(2) The problem of the material itself -- after the material enters the buffer bin, the segregation phenomenon of different degrees is generated. And after the material with uneven particle size distribution enters the roller press, the ends of the roller are unevenly stressed, and the deviation of the roll gap will be generated;
(3) One side of the lateral baffle fails, material throughput at both ends of the roller are uneven, the unrestricted side of the passage is large and the pressure is low;
(4) The deviation of the width of the inlet port along the direction of the roller is large or the side of the inlet is blocked by foreign matter, so that when the material passes through the gap between the two rollers, the throughput of the two ends of the roller is not equal.
6. Poor bearing cooling -- unsmooth cooling water circulation or insufficient cooling water may cause the bearing temperature to be too high and damaged.
7. For systems that use dry oil lubrication, bearing seal failure, insufficient dry oil supply, etc. may cause poor bearing lubrication and damage the bearing.
8. The oil deteriorates and the oil enters the ash, causing damage to the bearing.
To prevent bearing damage, do the following:
(1) Strictly control the quality when purchasing bearings;
(2) Ensure that the control system works normally and effectively;
(3) When the roller press starts feeding, it starts to add a certain pressure first. When the material pushes the roller press to open a certain roll gap, it starts to pressurize to the working pressure, so that the moving amount of the moving roller is not from the minimum to the maximum, which can effectively reduce vibration;
(4) When the bearing is installed, first, one must strictly control the interference of the bearing clearance; second, ensure that the centerline of the two rollers is parallel and at the same level; third, for different specifications of the roller press, the thickness of the stopper should also be different. When the roller press is idling, the two roller surfaces are not inconsistent. Generally speaking, it is suitable to be 18-30 mm;
(5) Regarding the working pressure, in theory, the best effective range is 30-150 MPa;
(6) In terms of materials, it is advisable to reduce the content of fine powder as much as possible, and the content of particles with a particle size of 20-25 mm need to be more than 60%;
(7) Take measures to control the deviation of the roll gap, such as adding a distributor in the upper part of the stable silo, adding the overflow box inside, and adding the insulation board in the warehouse;
(8) Ensure that the throughput of materials can be adjusted freely;
(9) Strengthening lubricant management and on-site management. Standard equipment management and a good environment are necessary to ensure the normal operation of the lubrication system.
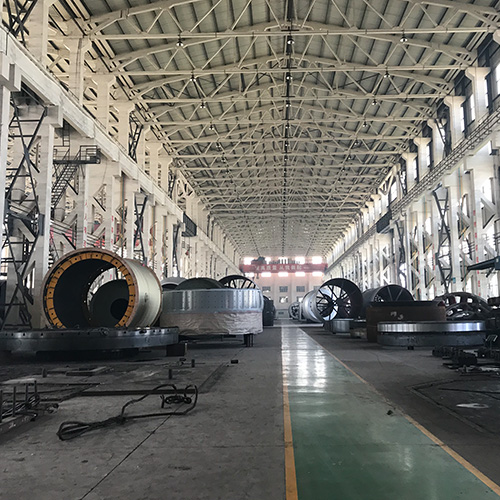