How to Choose the Right Type of Filter Bags in Different Conditions
Filter bags are the key and heart of the de-dusting collector/house in any industry plants. The de-dusting efficiency relies on the filter bag's right material, design and manufacturing. The right filter bag for the dust collectors/houses should be very effective for dusting collecting and removal and long service life. We suggest end users to choose the right type of filter bags with consideration of these conditions: the temperature of the exhausted gas, humidity, chemical property, size range of the dust, dust content, velocity of filtration (m/min), ash removal methods.
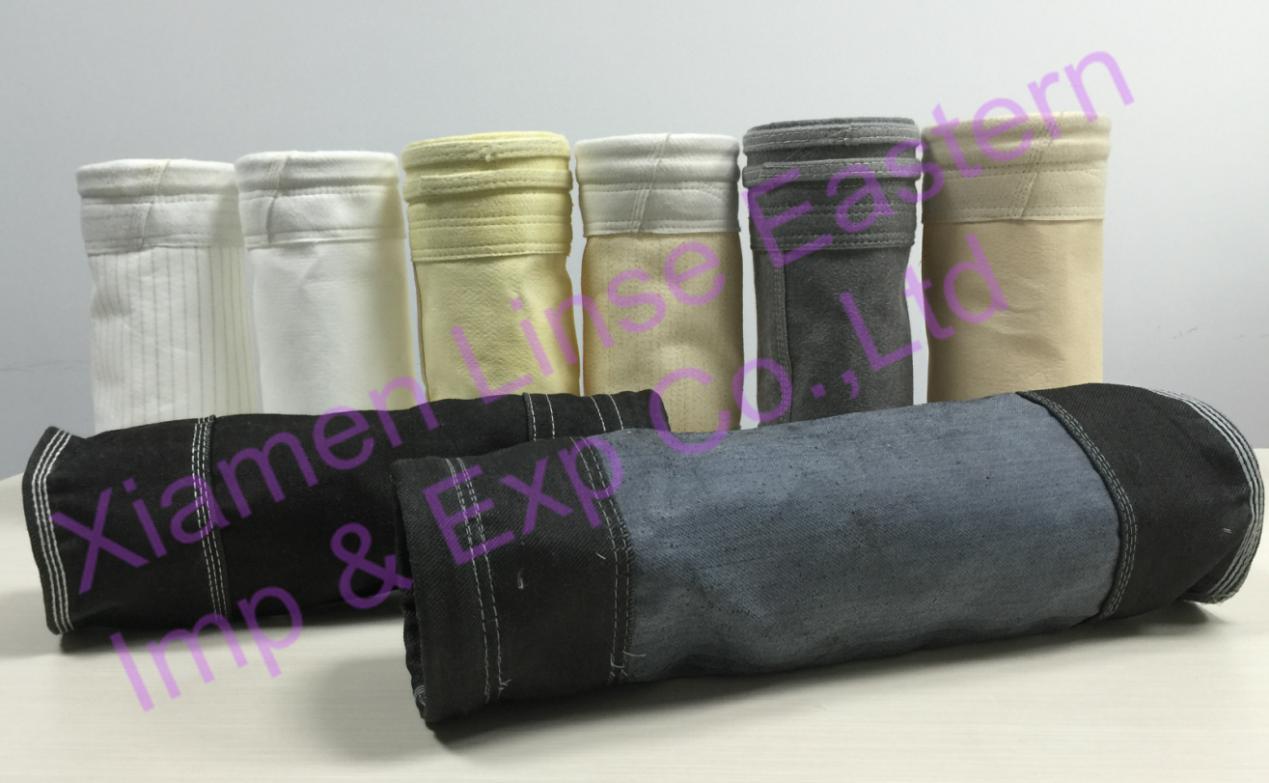
1.The principles and cautions of choosing filter bags
First, the filter bag should be with good performance under typical conditions of your dust collectors and exhausted gas.
Second, the filter bags should be used long enough because the long service life of filter bag can save your running costs and with better efficiency of the plants running.
Third, higher prices of bags do not equal to better performance in plan’s running. Choosing filter bags should consider the characteristics of the exhausted gas and filtration machinery comprehensively.
Fourth, the temperature of the gas, the corrosive gas content, the flammable gas content are key factors for choosing filter bag.
2.Choosing based on the characteristics of exhausted gases
We divide the exhausted gases into two categories taking 130℃ as the boundary. There are technical requirements about working temperature and maximum temperature when choosing filter bags. Filter bags will soon be deformed or melted if they are used under the maximum temperature for more than ten minutes per day.
The static electricity could be produced when the relative humidity is below 30%. Bag collectors/houses would perform better when the relative humidity is 30%~80%, but condensation will be caused if the relative humidity is more than 80% and temperature is over 130℃, especially when sulfur trioxide (SO3) is contained. Furthermore, the condensation will cause scale formation, dust blocking and rusty structure of filter bags, which would also damage the filtration machinery.
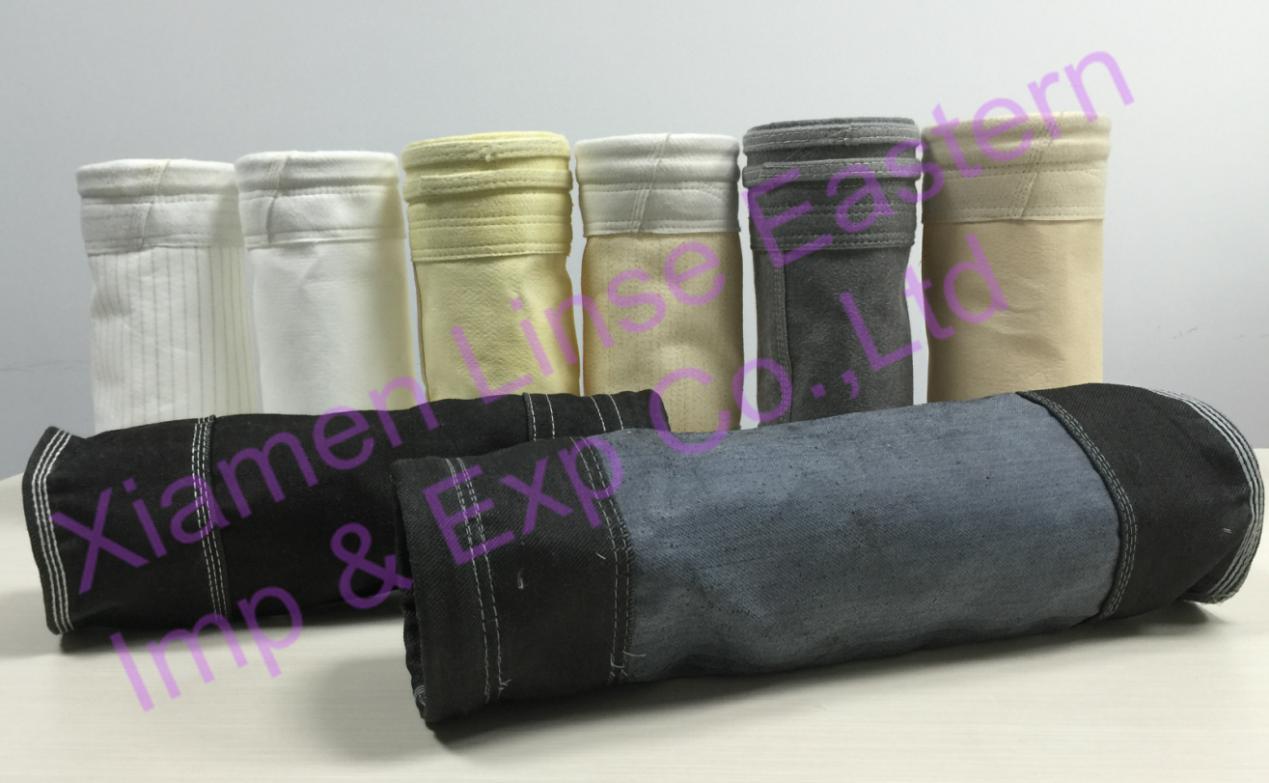
1.The principles and cautions of choosing filter bags
First, the filter bag should be with good performance under typical conditions of your dust collectors and exhausted gas.
Second, the filter bags should be used long enough because the long service life of filter bag can save your running costs and with better efficiency of the plants running.
Third, higher prices of bags do not equal to better performance in plan’s running. Choosing filter bags should consider the characteristics of the exhausted gas and filtration machinery comprehensively.
Fourth, the temperature of the gas, the corrosive gas content, the flammable gas content are key factors for choosing filter bag.
2.Choosing based on the characteristics of exhausted gases
We divide the exhausted gases into two categories taking 130℃ as the boundary. There are technical requirements about working temperature and maximum temperature when choosing filter bags. Filter bags will soon be deformed or melted if they are used under the maximum temperature for more than ten minutes per day.
The static electricity could be produced when the relative humidity is below 30%. Bag collectors/houses would perform better when the relative humidity is 30%~80%, but condensation will be caused if the relative humidity is more than 80% and temperature is over 130℃, especially when sulfur trioxide (SO3) is contained. Furthermore, the condensation will cause scale formation, dust blocking and rusty structure of filter bags, which would also damage the filtration machinery.
![]() Dust pasting on filter bags
|
![]() |
Damage caused by dust pasting |
① Under high temperature and high relative humidity conditions of exhausted gases, fiberglass filter bag, which has efficient ash removal characteristic, is a good choice. The finish treatment of the filter bag like silicon oil dipping, PTFE surface coating can achieve water-proofing, oil-proofing effects which are key features for the filter bag under high temperature and high relative humidity gas conditions.
② Polyester fiber, P84 fiber filter bag could hydrolyze when filtering high-temperature and moist gases.
③ Round-shaped filter bags are with better performance in high-moisture gases.
④ The temperature of the gas in inlet port should be more than 30℃ in order to avoid dust pasting on the filter bag.
⑤ Exhausted gases with high temperature and high moisture are prone to cause chemical reaction. For example, the polyester filter bag is stable when the temperature is below 130℃ but not stable when temperature is higher than 130℃. PPS fiber filter bag are with high temperature resistance, acid and alkali resistance but easy to hydrolyze. PTFE fiber is the king plastic fiber with the best chemical-resistance performance but it has the highest price among all the materials of filter bags. Therefore, choosing filter bag should comprehensibly consider of the characteristics of exhausted gases and the costs of filter bags.
3.Choosing bases on the dust property
First, the moisture and stickiness of dust
High-moisture and sticky dust in gas could paste on the surface of filter bag and cause seriously damage to the filter bag and the machinery. And CaO, CaCl2, KCl, MgCl2, NaCO3 in high moisture condition will react with H2O, or dissolve and ionize. Under those conditions, smoothing surface of the filter bag and water-proofing ability are required. Finishing treatment like singeing, calendaring can make the surface smooth so as to avoid moist and sticky dust damage the filter bag and machinery.
Second, in flammable gases
Coal dust, coke powder, aluminite powder, magnesium powder, etc. have the potential risk of explosion. Stainless steel fiber or modified chemical fiber is needle punched into the filter bag to avoid explosion risk.
Third, the liquidity in frictional dust collecting
Exhausted gas with high liquidity and friction could also damage filter bags, like silicon powder, aluminite powder, coke powder, carbon dust, sintering ores.
The wear and tear on dust removal bags due to the liquidity and friction of the dust are in various forms. According to our experiences in filter bag running sector, most of friction damages of filter bag are in the bottom or near bottom section. This is because the gas flow direction is from bottom to top and the flowing gas contains less dust around the top of the filter bag. The gas flow speed should be controlled so as to prevent crucial damage of filter bags.
For bag application in high liquidity in frictional dust collecting, we have suggestions as follows:
① Chemical fiber filter bags have better performance than fiberglass filter bags in these conditions.
② Needle punched filter bags are with better strength in frictional dust collecting.
③ Finishing treatment like coating, calendaring can enhance anti-friction ability of filter bags. For fiberglass filter bag, silicone oil dipping, graphite treatment, PTFE treatment can also strengthen their anti-friction ability. But when coating finishing treatment is used in high frictional dust collecting, the coating layer could be damaged in a short period.